DHS
PURLINS
- G500
G450
- <1.5mm - 500
>1.5mm - 450
- Z 275
- Fastbrace
Bolted Brace Channel
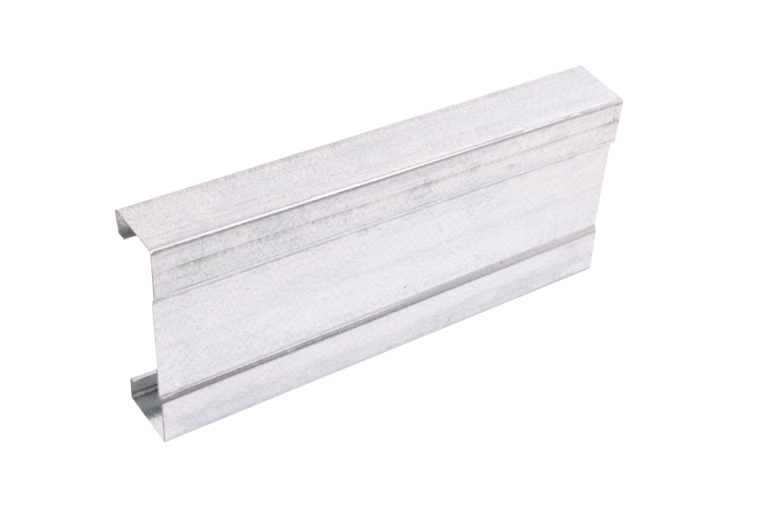
Overview
The Dimond Structural DHS purlin range is available in 12 sizes from DHS 150/12 to DHS 400/20 to suit commercial applications from 5m to 18m spans. Speed of installation is assured as DHS purlins and girts are supplied complete with brace channels ready for site assembly.
Material Specification
Dimond Structural DHS Purlins are manufactured by roll forming galvanised steel coil produced to AS 1397.
BMT - Base Metal Thickness
Z450 zinc weight coil can be supplied with order lead times of up 12 weeks. Contact Dimond Structural on 0800 DIMOND (0800 346 663)
Tolerances
Length:
- DHS Purlins ± 6mm
- Bracing System ± 2mm
Depth/Width:
- DHS Purlins ± 2mm
- Bracing System ± 1mm
Holes Centres: ± 1.5mm
Web/Flange Angle: 89-93 degrees
Components
Fastbrace
Fastbrace is a lock-in bracing system which runs in continuous lines between all purlins/girts and uses cleats with specially shaped lock-in tabs attached to each end of 89mm x 1.15mm (89/12) brace channel, suitable for use with DHS purlins from DHS 150/12 up to DHS 400/20. Fastbrace is fitted each side of the DHS purlin through pre-punched 18mm diameter round bracing holes, locking together to lower erection time. When a line of Fastbrace has been installed, the system provides resistance to restrict lateral movement of the DHS purlin system.
The end brace at the first and last bracing position is secured using the standard bolted connection on the outermost cleat end.
To ensure straight alignment of the bracing system, the bracing holes can be offset from the bracing line by 25mm over the last purlin spacing to accommodate the bolted cleat. If not, an angle of approximately two degrees from a straight alignment on the end braces is created.
Cranked Sag Rods are used in the lower bolt position to tie the bracing lines each side of the rafter together at the ridge (or at a step in the roof).
Where back to back DHS purlins are used, bolted end brace components are required each side, where the bolts can accommodate the extra purlin thickness, spacer cleats etc.
For use, handling and maintenance guidelines, refer to Environments 2.1.3, Handling And Storage 2.5.2 and Maintenance 2.1.6 of Purlin Systems Manual.
Fastbrace Components
Standard Brace
This is the standard Fastbrace component used almost everywhere in the system. It locks into other standard brace components, adjustable brace components, or end brace components.

End Brace
End brace is used at the end of a purlin bracing line, i.e. eaves or ridge, each side of a roof step, or at top and bottom girts on a wall. The end brace locks into either standard or adjustable brace at one end and is twisted between the purlin lips and bolted into position at the other end.

Adjustable Brace
This is the adjustable component in the Fastbrace system and is used where some level of adjustment on the purlin line is required. The purlin is adjusted into line and the 12mm diameter hex flange bolts on the brace tightened. The adjustable brace offers up to 20mm of adjustment.

Adjustable End Brace
Where the end purlin spacing is less than 800mm, an adjustable end brace with a bolted end cleat is available, as twisting of the end cleat is not practical. The adjustable cleat can be rotated up to 15 degrees from normal, to accommodate the change in angle from vertical portal to the roof slope of the rafter.

Bolted Brace Channel
Bolted Brace Channel is a bolted bracing system running continuously between all purlin/girt lines, which uses cleats clinched to each end of 89mm x 1.15mm (89/12) bracing channel, fastened with bolts through the DHS purlin (two bolts each end). Bolted Brace Channel is suitable for use on all DHS Purlin sizes.
Cranked Sag Rods are used in the lower bolt position to tie the bracing lines each side of the rafter together at the ridge (or at the step in the roof).
For use, handling and maintenance guidelines, refer Environments 2.1.3, Handling And Storage 2.5.2 and Maintenance 2.1.6 of Purlin Systems Manual.
Bolted Brace Channel Components
Bolted Channel Brace
This is the standard component used in the bolted channel bracing system and is used almost everywhere.

Adjustable Bolted Channel Brace
This is the adjustable component in the bolted brace channel system and is used where some level of adjustment on the purlin line is required.
The purlin is adjusted into line and the hexagonal flange bolts on the brace tightened. The adjustable brace offers up to 20mm of
adjustment.

Brace Channel Section Properties

Tabulated properties are based on full unreduced sections.
Note: Mass assumes a total coated weight for the zinc coating of 450 g/m2
C100/19 Purlin
Dimond Structural can supply a C100/19 Cee section (100mm x 50mm x 1.85mm BMT) for economy as a small section purlin or girt. Any limitation placed on the design and use of the Dimond Structural Purlin Systems as detailed in the Purlin Systems Manual also apply to the C100/19 Purlin. C100/19 purlins are typically braced with Sag Rods.
Design information for the C100/19 purlin can be provided by contacting Dimond Structural on 0800 ROOFSPEC (0800 766 377).
Portal Cleats
Portal Cleats are supplied by the fabricator or installer and welded onto the portal frame. Cleat thicknesses generally range from 6mm to 12mm thickness. The hole centres are laid out to suit hole punchings in the DHS purlin, refer CAD Details. The cleat height may need to be increased where an expansion step in the roof is detailed.
General Purpose Bracket
General Purpose Brackets are supplied by Dimond Structural and are typically used to connect trimmer purlins etc. General-purpose brackets are not load rated and are suitable for application only in non-structural elements. Holes and cleat dimensions are set-out to suit use with the DHS Purlin System only, refer CAD Details
Sag Rods
Purpose-made cranked sag rods are installed at each bracing line in the lower holes on the DHS ridge purlins to tie the bracing lines on each side of the rafter together at the ridge. Sag Rods are fully tightened up upon installing purlin bracing.
Supplied by steel erectors and fabricators in 12mm diameter engineering round bar Grade 250MPa, galvanised or electroplated finishes, with double nuts and washers each end. Where loads require, 16mm diameter engineering round bar can be used.
Timber Battens
Where Timber Battens are to be fastened to the DHS Purlin System, Dimond Structural recommend using an ex 50mm x 50mm timber batten or a depth of batten to account for insulation and ventilation requirements, gauged two sides and treated to H3.1 timber preservation such as boric or LOSP (low organic solvent preservative). Avoid the use of CCA treated timber, as chemicals used in the CCA treatment (e.g. copper and chromium) could contact the galvanised purlin surface and the fasteners, causing dissimilar metal corrosion.
The batten is fixed onto the top flange of the DHS Purlins, once the netting or safety mesh has been laid on the structure. For ex 50mm x 50mm battens, fixings are to be 10g – 16 x 75mm Countersunk Rib Head Wingteks. The coating finish is a zinc plated AS 3566 class 2 finish. Longer, other types of fixings may need to be considered when the timber depth is greater.
Spacing of the Wingteks is dependent on the DHS material thickness it is being fixed into. To achieve a maximum outward load of 5.0kN/m on the Timber Batten, refer to faster centres in the following table.
BMT - Base Metal Thickness
Specific Design
Design Basis
Dimond Structural DHS Purlin Systems have been designed to comply with AS/NZS 4600:1996, based on physical testing and analysis carried out by the University of Sydney, who are recognised for their expertise in the area of cold form design. The structural analysis consisted of several modules including cross-sectional analysis, an AS/NZS 4600:1996 design module, inplane structural analysis, and finite element lateral buckling analysis.
Methods in AS/NZS 4600:1996 for determining pure shear, combined bending/shear, lateral buckling and distortional buckling have, in some cases, resulted in lower purlin capacities than previously published. These are included in the design tables in the Purlin Systems Manual.
Appropriate design load combinations for each Limit State should be determined in accordance with AS/NZS 1170. It is recommended these be expressed as uniformly distributed bending loads (kN/m) assumed to be acting in-plane applied about the major axis of symmetry (X-X) and uniform axial compression loads (kN) applied about the rotational axis (Z-Z) for direct comparison with the tabulated data in this manual.
Self weight of the DHS Purlin Systems is not included in any load tables and must be calculated as part of the total dead load of the building elements supported by the purlin.
DHS Purlin System Design Considerations
Data presented in the Purlin Systems Manual is intended for use by structural engineers. Load situations other than uniformly distributed and axial loads will require specific design.
Design capacity of the DHS Purlin System is largely dependent on the amount of restraint provided to the purlin section. Data presented in DHS Purlin System Load Span Tables 2.3.4 assumes that bracing prevents both lateral movement and rotation of the section at that point.
Design Capacities in the Limit State format have been derived by the application of a capacity factor, Φ:
Bending Φb = 0.90
Compression Φc = 0.85
A design yield strength of 500 MPa has been used for DHS purlins and girts. This is in line with the minimum specified yield for G500 material and is less than the consistent minimum yield stress in the G450 material used in manufacture.
Tables in the Purlin Systems Manual are intended for use where roofing or cladding is attached to one DHS purlin or girt flange, where it is assumed that the screw-fastened cladding significantly prevents lateral movement of the flange to which it is attached. Where this assumption does not hold, it is recommended that the number of braces required is specified such that the purlin load capacity, ΦbWbx is not less than the capacity for the Fully Restrained (FR) case.
Gravity type loads can be assumed to act perpendicular to the roof plane for roof pitches up to 10 degrees provided the DHS purlins are placed with their flanges facing up the slope. For roof pitches greater than 10 degrees, load components about the minor axis of symmetry (Y-Y) should also be considered.
Span Guide
As a guide, single spans are used most frequently, particularly where purlins/girts are set down between the rafters/columns.
Deflections may govern on larger spans.
End and internal continuous configurations may be used where lower deflections are required.
Lapped end and lapped internal configurations are more economical on large purlin spans where better strength and lower deflections are required.
Deflection Guidelines
As a guide to acceptable deflection limits for serviceability of the DHS Purlin System used as purlins or girts, the following limits are recommended for wind load and dead load actions,
- Where there is no ceiling:
- Deflection for Ws≯ Span/150
- Deflection for G ≯ Span/300
- Where there is a ceiling:
- Deflection for Ws ≯ Span/200
- Deflection for G ≯ Span/360.
For further guidance on deflection limits, refer to AS/NZS 1170.
Bracing Guidelines
For roofs, the out of plane component of the dead load of the roofing and purlins is assumed to be carried in tension by Fastbrace or Bolted Brace Channels tied across the ridge or into the ridge beam for monoslope roofs. In order to minimise lateral deflections to purlin members, we recommend a maximum spacing between bracing lines and/or support framing of 3.5 metres.
For walls, the following table gives the maximum allowable wall heights for Dimond Structural bracing systems, where the dead load of cladding and girts is assumed to be carried in tension to an eaves beam by Fastbrace or Bolted Brace Channels.
In order to minimise deflections in the girt member, we recommend a maximum spacing between bracing lines and/or support framing of 3.5 metres.
Specific design of the bracing system and connections is required for wall heights greater than the limits shown or where the bracing is designed to carry compression loads.
BMT - Base Metal Thickness
Basis to table: 1) Maximum spacing of bracing lines/portal frames 3.5m and 2) Maximum cladding weight 6.7kg/m2
Specific Design
Specific design to AS/NZS 4600 is required where DHS purlins -
- have suspended loads present (such as ducting and piping). Suspended loads are connected to the DHS purlin web or, if this is not possible, to the DHS purlin bottom flange within 25mm of the web. Under no circumstances should loads be hung off the purlin lips.
- are used as cantilever members.
- are used as truss or portal members.
- have holes larger than standard bolt holes present.
- are subject to out of plane loading about the minor Y-Y axis.
For further specific design details refer to section 2.3 Specific Design - DHS Purlin System in Purlin Design manual
Load Span Tables
Download DHS Purlin Load Span Tables
Purlin Systems Durability
View Dimond Purlin Systems durability statement
Relevant Product CAD Details
Below you will find all of the relevant product CAD technical details in .dwg, .pdf & .rvt format.
If you have any questions regarding the details below please contact one of our technical team on 0800 550 660
Product Technical Statement
To help you get through the building consent process as quickly as possible, we have developed the Product Technical Statement (PTS) downloads to make it quick and easy for specifiers to access the documentation required.
The PTS downloads hold all of the information the council requires for a building consent where Dimond product is specified.
More Products
Top Notch Purlins
Dimond’s range of Top Notch purlins are compact, lightweight and easy to install. They are ready for use in many smaller spanning applications from 2m to 7m. Top Notch purlins come in a full range of sizes from 60mm to 150mm depth, easily tek screwed to the supports without the need for purlin bracing and cleats.